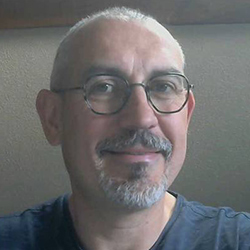
Poste de travail et activité de maintenance sont étroitement liés. Quels risques peuvent être encourus ?
50% des accidents rencontrés dans les métiers de maintenance sont dus à des énergies (électrique, hydraulique, pneumatique, mécanique…) mal maîtrisées pendant des interventions.
Trois grandes causes sont à traiter pour progresser :
- organisationnelles,
- techniques,
- humaines (comportementales et managériales).
Le personnel de production et les prestataires extérieurs qui réalisent des actions de maintenance sont également concernés car il ne s’agit pas de considérer la seule affectation à un poste de travail, mais surtout de regarder les tâches et activités réalisées. L’AFIM, Carsat et l’INRS ont réalisé une analyse sur l’accidentologie démontrant une occurrence d’accidents jusqu’à 3 fois supérieure à la moyenne pour les activités de maintenance, avec un taux de mortalité jusqu’à 8 fois supérieur.
Dans le secteur industriel, les chutes de plain-pied (en termes de fréquences) et les maîtrises d’énergies (pour la gravité) sont difficiles à résorber. Du point de vue réglementaire, seule la norme NF C18-510 sur l’électricité et le code du travail étaient à la disposition des acteurs de la maintenance avant la publication de la norme NFX 60-400. La directive machine, quant à elle, évoque le sujet de la maintenance à la marge et de manière très globale.
Comment peut-on sécuriser les interventions de maintenance ?
Techniquement, lorsque se pose la question d’une intervention en sécurité pour une opération de maintenance, il convient de considérer toutes les énergies et fluides en présence, et pas seulement l’électricité. Lors de la mise en œuvre de la démarche on doit s’intéresser à tous les risques professionnels directs et indirects liés aux énergies et fluides. C’est la donnée d’entrée qui permet de définir les mesures de mise en sécurité les plus efficaces. Dresser une « check-list » qui soit une véritable clé d’entrée pour l’analyse des risques systématique préalable à chaque situation de maintenance est une bonne pratique à mettre en œuvre.
Les contraintes et causes habituelles de défaut de maîtrise de ces risques en maintenance sont :
- le manque d’informations (ex : plans obsolètes),
- les défaillances de communication (ex : entre équipes production et maintenance, au passage de consigne entre équipes…),
- les installations vétustes,
- les problèmes d’accessibilité,
- les problèmes de conception (et de modification non contrôlée),
- le manque de fiabilité des organes de sécurité et des moyens de blocage,
- le défaut d’entretien (ex : pas de plan préventif de l’équipement ou des organes de mise en sécurité),
- les idées reçues (appuyer sur un bouton d’arrêt d’urgence ne met pas forcément l’agent en sécurité si les flux énergétiques ne sont pas pris en compte).
La maintenance n’est pas tributaire des seules considérations techniques. Les contraintes organisationnelles et comportementales jouent un rôle important.
Comment concilier urgence de l’intervention et sécurité ?
Il faut trouver une solution rapide pour ne pas bloquer un flux de production trop longtemps. En dépannage urgent, 80 % de la sécurité des opérations de maintenance repose sur un bon comportement de l’opérateur. Il faut s’inspirer des pompiers qui s’entraînent et ont des protocoles systématiques dans l’approche du risque pour ne pas céder à la pression et commettre une erreur.
Le comportement de chacun est une équation résultant de l’individu, mais aussi de la culture d’entreprise, des pratiques des managers et de l’organisation. Deux types de profils comportementaux « à risque » existent : le jeune débutant (forte fréquence d’accidents, peu de gravité) ou l’expert qui s’est accoutumé au risque, génère peu d’accidents mais avec une forte gravité. La production, partenaire de la maintenance, doit être impliquée dans la démarche, de même que l’encadrement et la direction. L’implication de la hiérarchie est primordiale car les comportements, et donc le succès des mesures de sécurité pour la maintenance, se gèrent sur le long terme.
Pour les interventions programmées (typiquement le préventif), il est possible par la préparation d’optimiser à la fois durée d’arrêt des machines et sécurité. La démarche Apave insiste sur l’intérêt de revenir aux bonnes pratiques de maintenance (ratio maintenance subie/préparée, méthodes, fiabilisation, maintenabilité…) pour gagner à la fois en sécurité et en performance.
Concernant la norme NFX 60-400, quelles évolutions propose-t-elle ?
La commission de normalisation a travaillé en capitalisant sur les expériences croisées de l’AFIM, d’APAVE et de l’INRS et a pris en compte les contraintes techniques, organisationnelles et humaines. La norme ne se base pas seulement sur des expériences franco-françaises mais s’inspire de démarches internationales comme le Lock Out Tag Out (LOTO), ou le Lock Out – Tag Out – Try Out (LOTOTO).
Le recensement des sources d’énergies, le choix de processus de mises en sécurité, le principe d’analyse de risques, la localisation de dispositifs de blocage, la mise en place de « cadenassage » sont autant de mesures opérationnelles proposées par la norme, auxquelles s’ajoutent des logiques de compétences, de formations, de qualifications. Elle donne des conseils spécifiques concernant les tuyauteries, la mécanique, intègre un logigramme, des modèles de fiches repères pour identifier les sources d’énergies dangereuses sur un équipement,…
L’analyse de risques est incontournable dans la mise en sécurité : savoir qui est responsable de la sécurité d’un intervenant peut s’avérer complexe. Imaginons une ligne de production bloquée un vendredi soir. Le week-end, on bascule en mode astreinte. Il n’y aura plus de chef d’équipe… La norme propose une trame à adapter selon les situations d’entreprises. Elle donne un cadre et des principes, et une réflexion adaptée à chaque contexte (avec le soutien d’un consultant Apave par exemple) doit déterminer l’organisation adaptée et efficace.
C’est l’analyse de risques qui indique ce qui doit être mis en place. Cinq processus de mise en sécurité sont notamment décrits dans la norme :
- l’isolation renforcée
- l’isolation simple enrichie de mesures compensatoires
- la neutralisation
- la mise en sécurité en fonctionnement (ex pendant la phase d’essai ou de diagnostic)
- le cadenassage
La norme NFX 60-400 opère sur la base du volontariat. Elle recommande la mise en place d’un système d’habilitation et de qualification dans l’entreprise. La personne ayant la vue d’ensemble de toutes les énergies est généralement celle qui a la compétence pour faire l’analyse de risque et ce n’est pas forcément un expert de toutes les énergies (ex : pas un électricien).
Les opérations récurrentes peuvent être traitées par des procédures standard. Pour le non-récurrent, la norme propose des procédures génériques qui encadrent les jalons de mise en sécurité, soutenues par des aides opérationnelles (plans à jour, listes des énergies en présence, localisations des énergies, chargés de consignation,…).
Quelles sont les évolutions auxquelles s’attendre pour la version européenne de cette norme ?
Près d’une dizaine de pays se sont impliqués, dont l’Allemagne, la Grande Bretagne et l’Italie. Le besoin d’une norme Européenne est confirmé. Sans préjuger du document final, forcément collectif, la norme repart de la NF X60-400 et l’améliore sur la forme (lisibilité) et le fond :
- Articulation avec les autres normes maintenance et sécurité
- Approche mieux intégrée de toutes les énergies
- Gestion de la zone de recouvrement production/maintenance (réglage, maintenance de niveau 1…)
- Surveillance et mise à jour d’une analyse de risque préparée (ex pour un préventif)
- Cas des modes dégradés…
La gestion du changement : véritable enjeu de la mise en sécurité ?
La démarche HOT LOTO améliore l'efficacité et la sécurité des opérations de maintenance grâce à la combinaison de leviers Humains, Organisationnels et Techniques.
Elle comprend des préconisations très opérationnelles. Technique : diagnostic de maintenabilité, fiche loto, management visuel des points de condamnation des énergies…. La mise en place de fiches repères LOTO par équipement contribue à changer les comportements. Organisationnel : des modèles de documents de traçabilité, une trame de procédure générale de mise en sécurité des énergies et fluides.
Reste à traiter l’axe majeur complémentaire à la technique et à l’organisation : le facteur humain… Pour ce faire nous apportons tout un catalogue de formations (mainteneurs, exploitants, accueil entreprises extérieures, comités de direction, préventeurs…) mais également une démarche projet soutenue par de l’accompagnement au changement, des actions sur le management et la culture-comportement sécurité.
La sécurité n’a pas de prix mais représente un coût ! L’arbitrage entre le coût d’une mise en sécurité et le gain en sécurité est un sujet délicat à aborder. La mise en place de la démarche HOT LOTO complète permet de minimiser à terme l’impact sur la performance telle le TRS (Taux de Rendement Synthétique), voire de générer un gain de performance grâce au retour aux bonnes pratiques de maintenance. Après mesure et analyse, le constat est frappant : sur du moyen terme, une bonne maintenance augmente la sécurité et également améliore le TRS.
En travaillant mieux, on gagne sur les deux tableaux alors qu’avant on transigeait parfois avec la sécurité pour favoriser une intervention rapide. L’optimisation du système de mise en sécurité (via les fiches repères qui cartographie les énergies, des modes opératoires pré-préparés...) minimisera le temps supplémentaire pris pour les interventions. Le meilleur moyen de ne pas se mettre en danger en dépannage, c’est de ne pas avoir de pannes en ayant fiabilisé les installations, en ayant prévu de la maintenance à la conception, en faisant de l’amélioration de « consignabilité » (maintenabilité).
A contrario, en l’absence d’approche globale et de gestion du changement, si on ne se met pas en mode projet, si on n’intègre ni les éléments humains et organisationnels, ni le management de la sécurité dans une réflexion à long terme, la démarche perdra en efficacité voire retombera dans le temps.
En conclusion, pouvez-nous dire ce que la démarche HOT LOTO améliore ?
Prenons l’exemple d’une démarche conduite chez un acteur agro-alimentaire :
Le secteur agro-alimentaire est compliqué car il nécessite beaucoup de maintenance, avec des délais très courts à cause du traitement des denrées périssables. Les marges sont faibles et les cadences élevées, avec des taux d’engagement d’installation très forts. Les équipes de maintenance interviennent sur des énergies très diverses, pas seulement électriques, mais aussi liées à la mécanique, aux fluides, à la température, à la pression, aux risques chimiques, etc. De nouvelles installations cohabitent avec des anciennes, non conçues pour travailler en sécurité pour la maintenance. Le fort taux d’accidentalité a amené cet acteur à mettre en œuvre la démarche APAVE HOT LOTO dans le cadre d’une politique Santé-Sécurité et de sécurisation de maintenance prenant aussi en compte l’impact sur la performance.
L’impact a été factuellement mesuré (indicateurs TRS et Risque résiduel) et a démontré que la démarche a permis d’allier les deux composantes risques et performance. La mise en place de fiches repères, d’un repérage des vannes, associé au travail sur les opérations récurrentes ayant des modes opératoires standards, a accéléré la mise en sécurité et a permis de fiabiliser les interventions et l’analyse de risques.
La démarche est toutefois fragile, la direction de l’entreprise doit être constante dans sa priorisation de la sécurité.
En résumé : L’analyse des risques est un préalable à la sécurisation des actions de maintenance. Plus que le poste, c’est l’activité dans sa globalité qu’il faut analyser tout en impliquant la direction. La norme NFX 60-400 et la démarche HOT LOTO APAVE proposent des process opérationnels permettant de concilier actions de maintenance et performance de l’entreprise. Montrer les coûts de mise en œuvre permet de dégager des moyens pour progresser et de gagner sur tous les plans, et de traiter le facteur humain par une gestion du changement efficace, en mode projet. Un effet collatéral de cette mise en œuvre : la détection de signaux faibles de dérives dans les process de l’entreprise.
Sur le même
thème